Knowledge and Skills for the Next Level of Operator
PROCESS | DICIPLINE | PERCEVERENCE | LEADERSHIP | SOLUTIONS
Leadership: The ability to see through and beyond the obstacles of challenges to form a vision and equip the mission with tools and solutions to persevere to the finish line.
Achieving operational excellence in today's rapidly evolving landscape requires more than just technical expertise—it demands a leadership approach that integrates self-awareness, strategic foresight, and advanced digital capabilities. As industries shift toward AI-driven automation and data-driven decision-making, the ability to navigate complexity with clarity and purpose becomes the ultimate differentiator. My leadership philosophy is built on aligning purpose with action, enabling teams to operate with discipline, adaptability, and an unwavering commitment to success. Through years of driving large-scale transformations, scaling global operations, and implementing world-class methodologies, I have honed a framework that ensures businesses achieve sustainable growth while embracing innovation. This page outlines the critical knowledge, functional skills, and guiding principles required for next-generation operations leadership—bridging strategy, execution, and continuous improvement to build resilient, high-performing organizations.
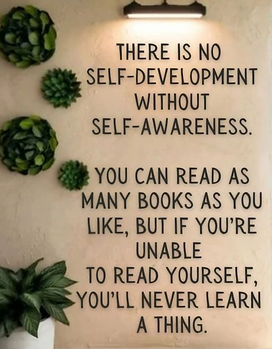
Functional skills for the next-generation operations leadership
Technical Skills
-
Digital Literacy: Mastery of digital tools and platforms for operational efficiency.
-
Data Analysis & Interpretation: Extracting actionable insights to drive business strategy.
-
Cybersecurity Awareness: Safeguarding information assets in an increasingly digital world.
-
Technical Project Management: Leading complex projects to deliver measurable outcomes.
-
AI & Automation Integration: Leveraging emerging technologies to optimize operations.
-
Strategy & Business Model Development: Creating scalable, future-proof business models.
-
Financial Acumen: Driving profitability through budgeting, investment, and cost optimization.

Self-Knowledge Skills
-
Self-Reflection: Continual assessment of leadership effectiveness and decision-making.
-
Resilience & Stress Management: Thriving in high-pressure environments and leading through uncertainty.
-
Continuous Learning Mindset: Adapting to change and fostering a culture of innovation.
-
Mindfulness & Presence: Enhancing clarity and impact in leadership interactions.
-
Authenticity: Leading with integrity and alignment to core values.
-
Emotional Intelligence: Understanding and responding to evolving human needs.
-
Effective Communication: Engaging teams through clear, impactful messaging.
-
Conflict Resolution & Mediation: Navigating disputes to build high-functioning teams.
-
Team Building & Motivation: Aligning teams with a shared vision and purpose.
-
Adaptability & Flexibility: Driving change management with agility.
-
Inclusive Meeting Facilitation: Ensuring diverse perspectives shape decision-making.
-
Coaching & Mentoring: Developing talent for long-term organizational success.
-
Leading with Culture: Embedding a high-performance culture that drives engagement.
Cummunicative Skills
Guiding principles of world-class operations excellence
Building a Scalable Operations Excellence Model
-
Establishing foundational systems, methodologies, and performance metrics.
-
Integrating cutting-edge technologies such as AI, IoT, and digital twins.
-
Aligning business processes with data-driven insights for continuous optimization.
Operational Discipline & Execution Frameworks
-
Daily Operational Routines: Gemba walks, huddles, and 5S audits.
-
Weekly & Monthly Reviews: KPI tracking, supply chain syncs, and performance assessments.
-
Quarterly & Annual Strategy Sessions: Long-term planning, innovation roadmaps, and leadership development.
Industry 4.0 & Advanced Manufacturing Systems
-
Adoption of ERP, MES, and SCM tools for seamless integration.
-
Implementation of AI-driven predictive analytics for decision-making.
-
Deployment of Lean, Six Sigma, and Agile methodologies for continuous improvement.
Key Performance Indicators (KPIs) for Operational Excellence
-
Production & Efficiency Metrics: OTD, OEE, and defect reduction.
-
Inventory & Supply Chain Metrics: Forecast accuracy, inventory turnover, and lead time optimization.
-
Financial & Profitability Metrics: EBITDA margin, cost-per-unit, and COGS reductions.
Operational Maturity Models: Scaling Across Business Stages
-
Greenfield Operations: Establishing best-in-class infrastructure from the ground up.
-
Turnaround Strategies: Stabilizing underperforming operations and restoring profitability.
-
Expansion & Growth Models: Scaling capacity while maintaining agility and efficiency.
-
Sustained High-Performance Operations: Embedding innovation and continuous improvement as a core function.


Transforming Business Through Data, AI & Advanced Operations
Throughout my career, I have led global supply chain transformations, SIOP integration, operational footprint optimization, and manufacturing advancements—leveraging data-driven strategies to drive efficiency, cost reduction, and scalability. From restructuring multi-billion-dollar supply networks to eliminating bottlenecks in high-growth environments, I have seen firsthand how master data, advanced analytics, and AI-driven modeling can redefine business performance. By integrating demand, logistics, materials, and geographically diverse capabilities across distribution (B2B & B2C), services, manufacturing, and processing, organizations can unlock unprecedented efficiency and agility.At Apple, Carrier, Juul, Peloton, and other industry leaders, I’ve implemented mathematical models and real-time algorithms that optimized global supply and distribution networks, streamlined manufacturing footprints, and reconstituted operating models to scale businesses at a world-class level. By eliminating redundant nodes in supply chains and enhancing value stream visibility, I have successfully helped organizations increase working capital, minimize inefficiencies, and accelerate market expansion. With today’s rapid advancements in AI-driven automation, digital twins, and real-time computing, companies that deploy these intelligent solutions can identify and correct tactical errors in real time, maintaining their competitive edge in an evolving global landscape. The race for operational excellence is in full force—those who embrace data and automation today will define the industry leaders of tomorrow.
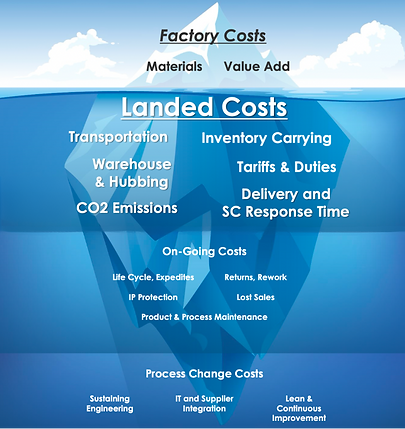
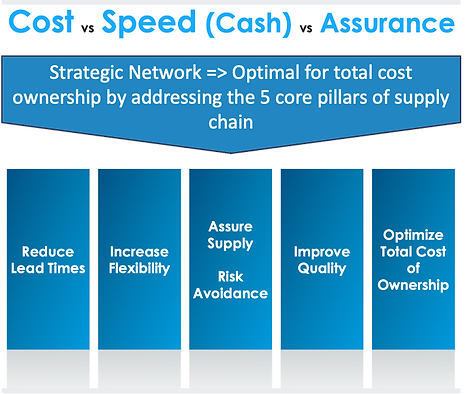
Deployment Approach: Transforming Business Through Data, AI & Advanced Operations
1. Building a Comprehensive Master Data Infrastructure
-
Implemented unified data architectures that consolidate real-time inputs across supply chain, logistics, and operational ecosystems.
-
Integrated demand, logistics, and material flow data into scalable digital platforms, ensuring real-time supply and production visibility.
-
Developed end-to-end supply chain synchronization across ERP, WMS, TMS, and advanced analytics platforms to enable dynamic decision-making.
2. Supply Chain Optimization & Distribution
-
EfficiencyLed AI-driven supply chain models that optimized distribution networks, reducing complexity while enhancing service levels and cost efficiencies.
-
Designed real-time demand sensing and fulfillment strategies, ensuring optimal inventory positioning across global B2B and B2C channels.
-
Developed node minimization strategies, eliminating inefficiencies in production, warehousing, and logistics to improve end-to-end throughput.
3. Operations Footprint Optimization & Value Stream Mapping
-
Drove manufacturing footprint optimization by aligning production capabilities with market demand, cost, and lead time requirements.
-
Applied lean methodologies and digital simulation tools to identify inefficiencies, reduce waste, and improve production velocity.
-
Led greenfield and brownfield site expansions, ensuring Industry 4.0 integration, smart automation, and scalable operational models.
4. Real-Time Analytics & AI-Driven Tactical Optimization
-
Deployed AI-powered control towers and digital twins, enabling real-time monitoring of supply chain health and operational efficiency.
-
Integrated predictive analytics and anomaly detection, allowing teams to anticipate disruptions and adjust strategies dynamically.
-
Developed autonomous optimization models that provided instant corrective actions on daily tactical execution errors.
5. Organizational Transformation & Workforce Enablement
-
Restructured organizational models to align with data-driven decision-making, increasing agility and cross-functional collaboration.
-
Automated key operational workflows, leveraging AI to streamline administrative, procurement, and production planning tasks.
-
Equipped teams with AI-driven decision-support tools, enabling faster, smarter, and more strategic execution at all levels.
6. Continuous Optimization & Future-Proofing for Competitive Advantage
-
Implemented self-learning AI models that continuously refine supply chain, operations, and manufacturing strategies.
-
Built cloud-based analytics dashboards, providing executive teams with actionable insights for cost reduction and market expansion.
-
Drove agility-focused innovation, ensuring adaptability to market disruptions, geopolitical shifts, and evolving consumer demand patterns.
THE BUSINESS & OPERATIONS ENGINE
Cyclical planning & processes
Operations management (OM) is the administration of business practices to create the highest level of efficiency possible within an organization. It is concerned with converting materials and labor into goods and services as efficiently as possible to maximize the profit of a business.

Planning
Determines what will be produced, by whom, & how & when. It formulates the plan for labor, equipment, work center, & material requirements needed for production.
Scheduling
Organizing
Supply Chain Purchasing
Scheduling emphasizes “when” the operation will be completed. It aims to make the most of the time given for the completion of the operation.
Organizing creates a task & authority structure for establishing a role structure & information flow within the operations subsystem. They assign authority and responsibility to achieve goals.
Purchasing is the process of buying parts or services to manufacture products from suppliers/vendors. It includes raw materials, machineries, consumables, etc
Controlling
Process of monitoring the actual performance in accordance with the planned performance. Some major areas for controlling are cost, quality, & schedule.
QA Mgt
QA (Quality Assurance): It emphasizes on defect-free products & ensures to deliver defect-free products to the customers.
QC (Quality Control): Quality control checks the quality of the goods produced against standards (Prevention action vs. Detection action).
Inventory Management
Inventory ManagementProcess of managing inventories from RM (Raw Materials) to FG (Finished Goods). Inventory management efficiently manages inventories to avoid both glut & shortages.
Maintenance Management
Ensuring machinery and equipment are in optimal working conditions. Implementing preventive and corrective maintenance schedules.
Major Roles Involved in OM
-
Operations Manager → Oversees daily production activities & ensures process efficiency.
-
Production Supervisor → Manages shop-floor operations & team performance.
-
Quality Assurance Manager → Ensures product quality and compliance with standards.
-
Supply Chain Manager → Handles procurement, logistics, and vendor relationships.
-
Maintenance Manager → Maintains equipment and minimizes downtime.
-
Data Analyst/Process Engineer → Tracks & analyzes PPC KPIs, recommending process improvements.
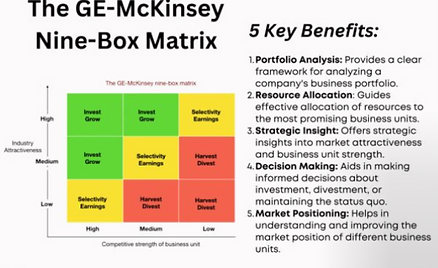
Other pertinent direct reporting roles, sometimes with shared responsibilities in larger organizations:
-
Human Resources → Manages employee recruitment, training, benefits, and organizational development. Ensures compliance with labor laws, promotes a positive workplace culture, and facilitates performance management and employee relations.
-
Finance → Manages budgeting, financial planning, cost analysis, and reporting. Ensures fiscal responsibility, cash flow management, and strategic investments to support business growth and profitability.
-
Continuous Improvement → Drives process optimization through Lean, Six Sigma, and other methodologies. Focuses on waste reduction, efficiency gains, and sustainable improvements to enhance productivity, cost savings, and quality.
-
Environment Health & Safety (EHS) →Ensures workplace safety, regulatory compliance, and environmental sustainability. Develops policies for hazard mitigation, emergency response, and occupational health programs to protect employees and the environment.
-
Legal → Provides guidance on regulatory compliance, contracts, intellectual property, and risk management. Ensures business activities align with laws and regulations to mitigate legal exposure and liabilities.
-
New Product Development → Leads innovation, product design, prototyping, and commercialization. Works cross-functionally to bring new products to market efficiently while meeting cost, quality, and customer requirements.
-
Sales → Drives revenue generation through customer acquisition, relationship management, and strategic market expansion. Aligns with marketing and operations to meet demand and deliver value propositions.
-
IT → Manages digital infrastructure, cybersecurity, and software solutions. Supports business operations with data management, system integrations, and technology-driven efficiencies.
-
Security → Protects company assets, employees, and information from physical and cyber threats. Implements security protocols, access control, surveillance, and risk mitigation strategies.
LEADERSHIP & BUSINESS ACCOUNTABILITY

Many leaders miss this crucial mindset shift…
They think:Leadership means giving orders.B
ut great leadership is something entirely different.
True leadership is about:
➟ Putting your team’s needs first
➟ Equipping them with the tools to succeed
➟ Supporting their growth and development
➟ Helping your team shine
➟ Encouraging rest and balance
➟ Offering clear guidance and constructive feedback
➟ Standing alongside your team—not above them
➟ Recognizing effort with genuine praise like, “Great job!”
Leadership is a journey, not a destination.
It means:
➠ Leading a business
➠ Leading yourself
➠ Leading others
➠ Leading teams
And the skills you need will keep evolving.
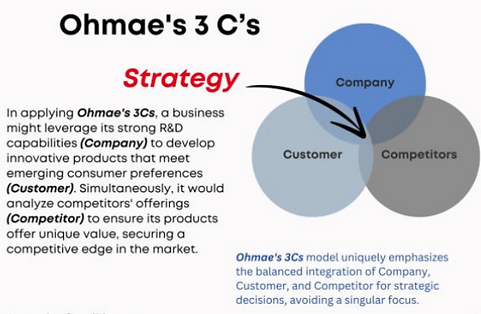
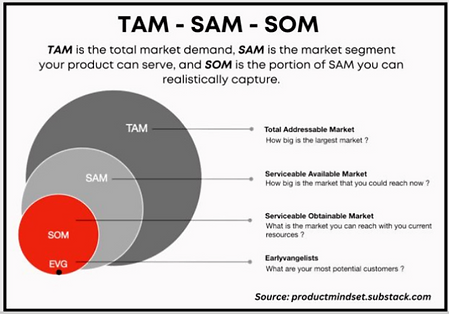
NPI- & EQUIPMENT QUALIFICATIONS
Manufacturing line buy off and qualification Process

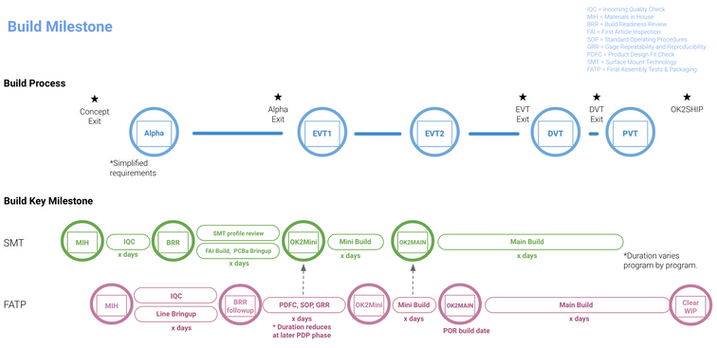
Consumer Electronics NPI Build & Qualification Process
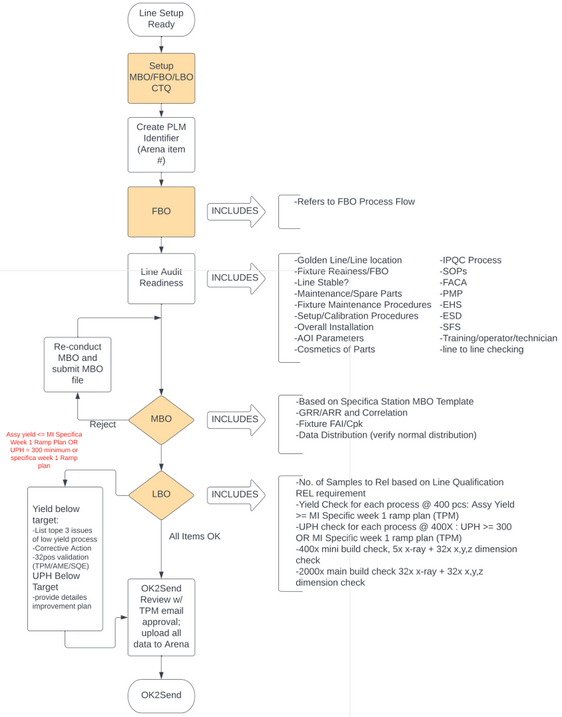
Manufacturing line buy off and qualification process steps